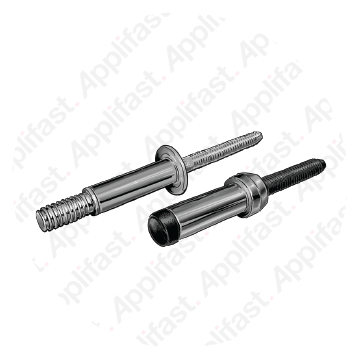
Structural Blind Fasteners
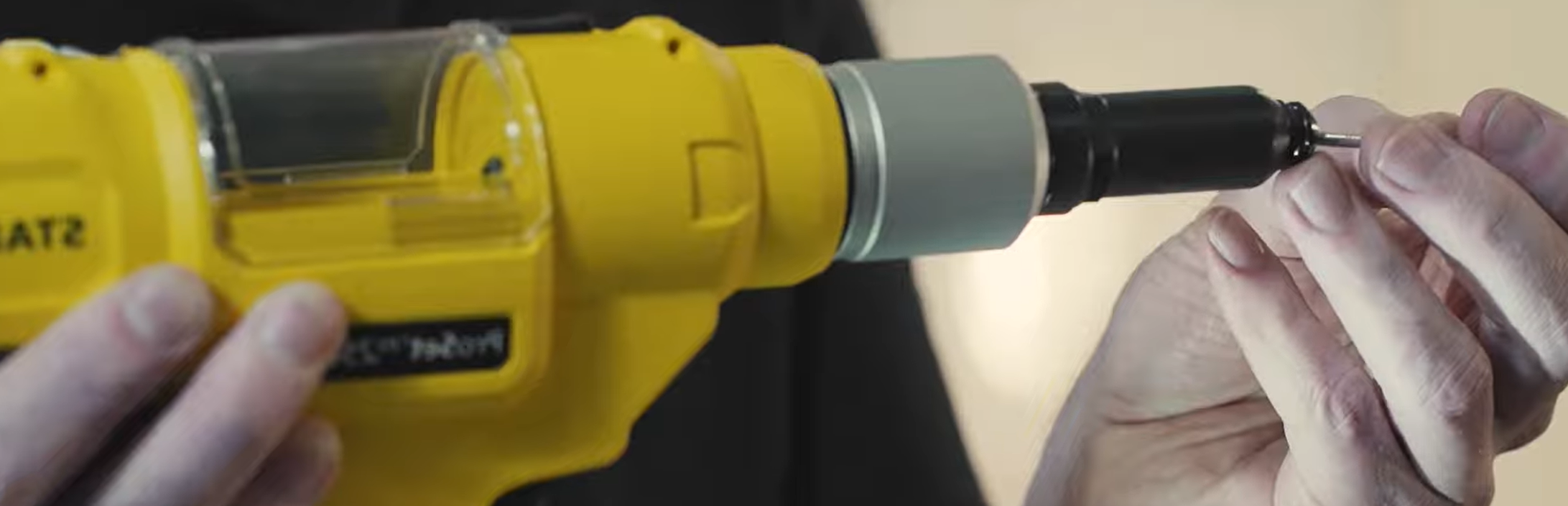
Structural Blind Rivets
Interested In Structural Blind Rivets?
Structural blind rivets are one-piece fasteners made from two assembled components. They ideal for applications with access to only one side of the material.
FAQs
Structural blind fasteners are engineered to deliver exceptional performance in extreme temperatures and harsh environments when appropriate materials are selected, corrosion protection measures are applied, and proper installation techniques are followed. They are manufactured from materials such as high-grade steel, stainless steel, and aluminum, known for their durability and resistance to corrosion.
We offer a wide range of structural blind fasteners, each designed to meet specific needs within industrial applications. This range includes steel and aluminum rivets with key features adapted to manufacturing challenges including heavy load and high vibration applications, installation in hard-to-reach areas, and hole filling applications that can seal the joint against water and salt.
Conventional riveting requires access to both sides of the workpiece for hammering or pressing the rivet into place. Structural blind rivets can be installed where the reverse of the workpiece isnβt accessible. Structural blind fasteners use a pulling mechanism that draws the fastener into place, securely clinching the material without the need for rear-side access. The installation process of structural blind fasteners offers advantages including accessibility, ease of installation, and speed.
There are many factors to consider when selecting structural blind fasteners. These guidelines help ensure the fastener chosen will provide the necessary strength, reliability, and performance for the intended use. Joint type and material thickness, load requirements, environmental conditions, installation constraints, grip range, and head style can all influence the decision. We provide expert consultancy to help you make the best choice for your project or process.